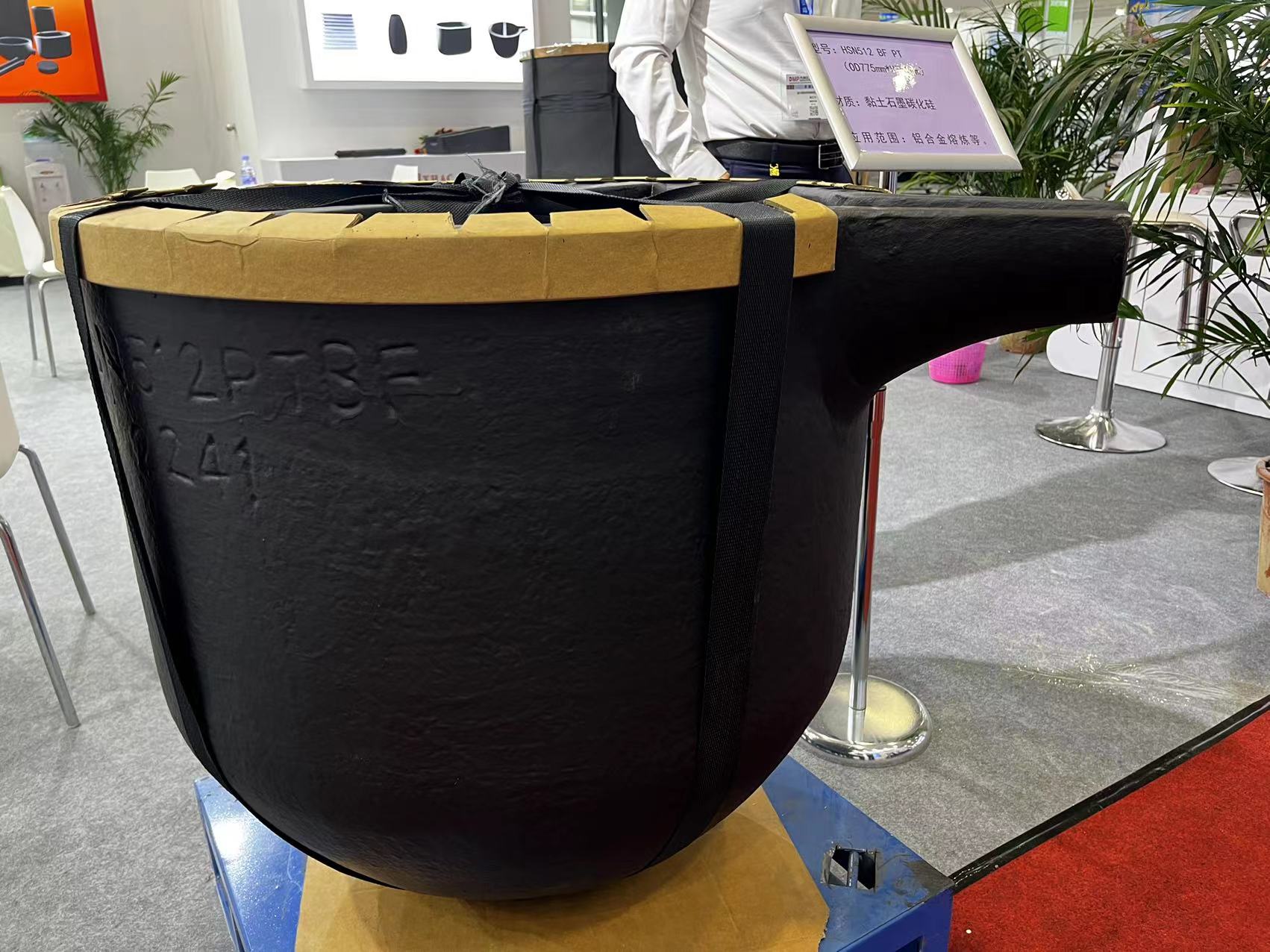
Forberedelsesmetoden til høj styrkegrafit silicium carbide crucibleTil smeltning af metal inkluderer følgende trin: 1) tilberedning af råmateriale; 2) primær blanding; 3) materialetørring; 4) knusning og screening; 5) forberedelse af sekundær materiale; 6) sekundær blanding; 7) tryk og støbning; 8) skæring og trimning; 9) tørring; 10) ruder; 11) primær fyring; 12) imprægnering; 13) sekundær fyring; 14) belægning; 15) Færdig produkt. Crucible produceret ved hjælp af denne nye formel og produktionsprocessen har stærk høj temperaturresistens og korrosionsbestandighed. Den gennemsnitlige levetid for Crucible når 7-8 måneder med en ensartet og defektfri intern struktur, høj styrke, tynde vægge og god termisk ledningsevne. Derudover forbedrer glasurlaget og belægningen på overfladen sammen med flere tørrings- og fyringsprocesser markant produktets korrosionsbestandighed og reducerer energiforbruget med ca. 30%med en høj grad af forglasning.
Denne metode involverer området for ikke-jernholdig metallurgi-støbning, især fremstillingsmetoden til højstyrke-grafit-siliciumcarbid-digel til metalsmeltning.
[Baggrundsteknologi] Speciel grafit-siliciumcarbidmuller bruges hovedsageligt i ikke-jernholdige metalstøbnings- og smedningsprocesser, såvel som i genvinding og raffinering af ædle metaller og produktionen af høj-temperatur og korrosionsbestandige produkter, der kræves til plastik, keramik, glas, cement, gumber og farmaceutisk fremstilling, som korrosionsresistente indeslutning i den petro, cement, gummi og farmaceutisk fremstilling, og som korrosionsresistiske indeholdende indhold i den petro, glas, cement, gumber og farmaceutisk fremstilling.
Eksisterende speciel grafit -siliciumcarbid -digelformuleringer og produktionsprocesser producerer produkter med en gennemsnitlig levetid på 55 dage, hvilket er for kort. Brugs- og produktionsomkostningerne stiger fortsat, og mængden af genererede affald er også høj. Derfor er det et presserende problem at løse en ny type speciel grafit -siliciumcarbid -digel og dens produktionsproces, da disse digler har betydelige anvendelser inden for forskellige industrielle kemiske felter.
[0004] For at løse ovennævnte problemer tilvejebringes en metode til fremstilling af højstyrke grafit-siliciumcarbidmuller til metalsmeltning. Produkter, der er forberedt i henhold til denne metode, er resistente over for høje temperaturer og korrosion, har en lang levetid og opnå energibesparelser, emissionsreduktion, miljøbeskyttelse og høj genanvendelseshastighed for affald under produktionen, maksimerer cirkulationen og anvendelsen af ressourcerne.
Forberedelsesmetoden til højstyrke grafit siliciumcarbidmuller til metalsmeltning inkluderer følgende trin:
- Forberedelse af råmateriale: Siliciumcarbid, grafit, ler og metallisk silicium anbringes i deres respektive ingrediensbeholder ved kran, og PLC -programmet kontrollerer automatisk udladningen og vejer hvert materiale i henhold til det krævede forhold. Pneumatiske ventiler kontrollerer udladningen, og mindst to vejningssensorer indstilles i bunden af hver ingrediensbeholder. Efter vejning placeres materialerne i en blandemaskine ved en automatisk bevægelig vogn. Den første tilsætning af siliciumcarbid er 50% af dets samlede beløb.
- Sekundær blanding: Efter at råmaterialerne er blandet i blandemaskinen, udskilles de i en pufferhopper, og materialerne i pufferhopperen løftes til blandingsbeholderen med en spand elevator til sekundær blanding. En jernfjernelsesindretning indstilles ved udladningsporten på spandhejs, og en vandtilsætningsanordning er indstillet over blandingsbeholderen for at tilføje vand under omrøring. Vandtilsætningshastigheden er 10L/min.
- Materiel tørring: Det våde materiale efter blanding er tørret i et tørreudstyr ved en temperatur på 120-150 ° C for at fjerne fugt. Efter fuldstændig tørring tages materialet ud til naturlig afkøling.
- Knusning og screening: Det tørrede klumpede materiale kommer ind i et knusnings- og screeningsudstyr til forknusning, og går derefter ind i en modangrebsknus for yderligere knusning og passerer samtidig gennem et 60-mesh screeningsudstyr. Partikler, der er større end 0,25 mm, returneres til genanvendelse til yderligere præ-knusning, knusning og screening, mens partikler, der er mindre end 0,25 mm, sendes til en tragt.
- Forberedelse af sekundær materiale: Materialerne i udladningshopper transporteres tilbage til batchemaskinen for sekundær forberedelse. De resterende 50% af siliciumcarbid tilsættes under den sekundære præparat. Materialerne efter det sekundære præparat sendes til blandemaskinen til genblanding.
- Sekundær blanding: Under den sekundære blandingsproces tilsættes en speciel løsning med viskositet til blandingsbeholderen gennem en speciel opløsning, der tilføjer enhed med en bestemt tyngdekraft. Den specielle løsning vejes af en vejende spand og føjes til blandingsbeholderen.
- Tryk og støbning: Materialerne efter den sekundære blanding sendes til en isostatisk pressemaskine. Efter belastning, komprimering, støvsugning og rengøring i formen presses materialerne i den isostatiske pressemaskine.
- Skæring og beskæring: Dette inkluderer skæring af højden og beskæring af digelburrs. Skæring udføres af en skæremaskine for at skære diglen til den krævede højde, og burrerne efter skåret er trimmet.
- Tørring: Crucible, efter at have været skåret og trimmet i trin (8), sendes til en tørringsovn til tørring med en tørringstemperatur på 120-150 ° C. Efter tørring holdes det varmt i 1-2 timer. Tørringsovnen er udstyret med et luftkanaljusteringssystem, der består af flere justerbare aluminiumsplader. Disse justerbare aluminiumsplader er arrangeret på de to indre sider af tørreovnen med en luftkanal mellem hver to aluminiumsplader. Kløften mellem hver to aluminiumsplader justeres for at regulere luftkanalen.
- Glasering: Glasuren fremstilles ved at blande glasurmaterialer med vand, herunder bentonit, ildfast ler, glaspulver, feltspatpulver og natriumcarboxymethylcellulose. Glasuren påføres manuelt med en børste under ruder.
- Primær fyring: Crucible med påført glasur fyres en gang i en ovn i 28-30 timer. For at forbedre fyringseffektiviteten indstilles en labyrintovnseng med en tætningseffekt og luftblokering på bunden af ovnen. Kilnesengen har et bundlag med tætning af bomuld, og over den tætningsbomuld er der et lag af isoleringsmursten, der danner en labyrintovnseng.
- Imprægnering: Den fyrede digel placeres i en imprægneringstank for vakuum og trykimprægnering. Imprægneringsløsningen transporteres til imprægneringstanken gennem en forseglet rørledning, og imprægneringstiden er 45-60 minutter.
- Sekundær fyring: Den imprægnerede digel anbringes i en ovn til sekundær fyring i 2 timer.
- Belægning: Crucible efter sekundær fyring er belagt med en vandbaseret akrylharpiksmaling på overfladen.
- Færdig produkt: Efter at belægningen er afsluttet, tørres overfladen, og efter tørring pakkes og opbevares diglen efter tørring.
Posttid: Mar-20-2024